Diamond Products
Eagle Bit’s are typically designated by series. Each series is designed to work under specific condions of ground
hardness and abrasiveness.
Please refer to the selection table to identify the appropriate series for your drilling conditions.
Eagle Bits are offered as a non-customizable design with a standard crown height and waterways.
Eagle Bits offer a great combination of quality and value.
SERIES 1/2
Eagle 1/2 is made with an extremely wear resistant matrix for long life in
soft formations, but can also be used in medium broken formations.
SERIES 3/4
Eagle 3/4 is a good choice for cutting soft to medium formations.
Recommended for low powered drills only.High loads will seriously reduce
bit life.
SERIES 5/6
Eagle 5/6 is a general purpose formula for cutting formations in the medium
hard range. 5/6 also works well in formations of variable hardness.
SERIES 7/8
Eagle 7/8 Series is a general purpose bit for cutting hard formations. For
hard competent and nonabrasive formations. This free cutting bit requires
high rotational speeds and light bit loads for best performance.
SERIES 9/10
Eagle 9/10 is made to cut ultra hard fine grain formations. This is an
alternative when drilling very hard formations with a low torque drill rig.
SERIES 11/12
Eagle 11/12 is made to cut ultra hard fine grain formations. This is an
alternative when drilling ultra hard formations with a low torque drill rig.
STANDARD WATERWAYS(S)
Standard waterways are recommended for most general purpose coring operations
and off great fluid circulation in a variety of conditions.
TURBO(T)
SON-MAK Turbo Bits waterways provide increased flushing ability and lessen the
contact area of the bit to the rock, therefore giving the bit more cutting ability with
less pressure. The allows for reduced torque and increased penetration rate. Only
avaible in impregnated diamond bits.
TAPERED WATERWAYS(TW)
Eagle 5/6 is a general purpose formula for cutting formations in the medium
hard range. 5/6 also works well in formations of variable hardness.
FACE DISCHARGE(FD)
Recommended for very soft and broken formations or when using Triple-tube (O3)
barrels SON-MAK Face Discharge waterways increase flushing characteristics to
prevent waterway blockage by ejecting fluid through ports molded into the face of
the bit.
DEEP I.D.WATERWAYS(DD)
Designed to maximize the waterway depth on the I.D of the bit, which reduces the
jetting or washing away of the core. The extra clearance minimizes the vacuum
effect caused by the water flow past the lifter case in a lost circulation application
SPIRAL(SP)
Recommended for drilling in broken formations. Specifically angled waterways
allow for greater fluid ejection.
1. Crown: Avaible in a wide variety of formations. The crown is the
cutting edge of the bit.
2. Tungsten Carbide: Protect stability of the crown.
3. Core Lifter Case Seat: Supports core lifter case when breaking core.
4. Bitthreads: Precision cut industry standart bit threads.
5. Bit Body: Made of superior quality steel and machined in small
batches to maintain manufacturing standarts.
6. Waterways: Controls fluid flow around the cutting edge of the bit.
7. Bit Face: Ideal design allow for quick startup of new bit.
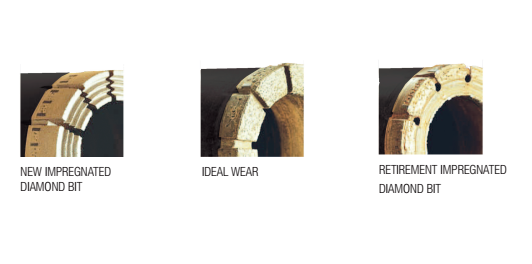
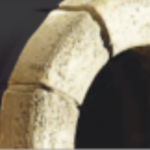
Sand blast face or use other recommended methods
to re-expose diamond. Try again with rpi (r/cm) in the 200/250 (80/100) range.
If the face glazes repeatedly, change to a higher bit

Possible Reasons:
• Excessive bit load; dropped rods; free fall of inner tube in dry hole
• Bit crushed by rod holder, foot clamp or pipe wrench
• Pushed down an undersized hole (i.e., reaming shell worn out).
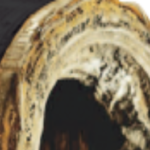
Possible Reasons:
• Lack of fluid.
• Too high of weight on bit being used.
Solutions
• Check pump and rod string for leaks, check
inner tube adjustment, maintain coolant flow
rates.
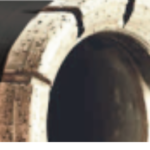
Possible Reasons:
• Often caused by excessive penetration
rate for the rpm used – rpi (r/cm) too low.
• Also can be caused by core grinding,
overdrilling.
Solutions
• Reduce penetration rate or increase RPM
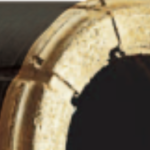
Possible Reasons:
• Overfeeding
• Broken formations
• Drilling over lost core
• Insufficient drilling fluid
Solutions
• Reduce penetration rate
• Cement or change to a lower series bit
• Check core barrel/core lifter/core lifter case
• Check inner tube length adjustment; check pump
and rod string for leaks – increase pump output
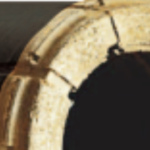
Possible Reasons:
• Lack of circulation
• Bit being reamed down under-size hole
• Vibratio
Solutions
• Increase coola
• Check reamer
under-sized
• Alter RPM
Corporate Video
